Blog
Incorporating Blast Freezing
At Scantec Refrigeration, we aim to meet if not exceed our clients’ expectations especially when their energy bills are off the charts.
A recent project that we completed, was a refrigeration system for a temperature-controlled logistics operator in Truganina, Victoria. The challenge of the project was the consolidation of three existing HFC-based refrigerated warehouses into one, with increased energy efficiency and reduced maintenance costs as published in HVACR Nation.
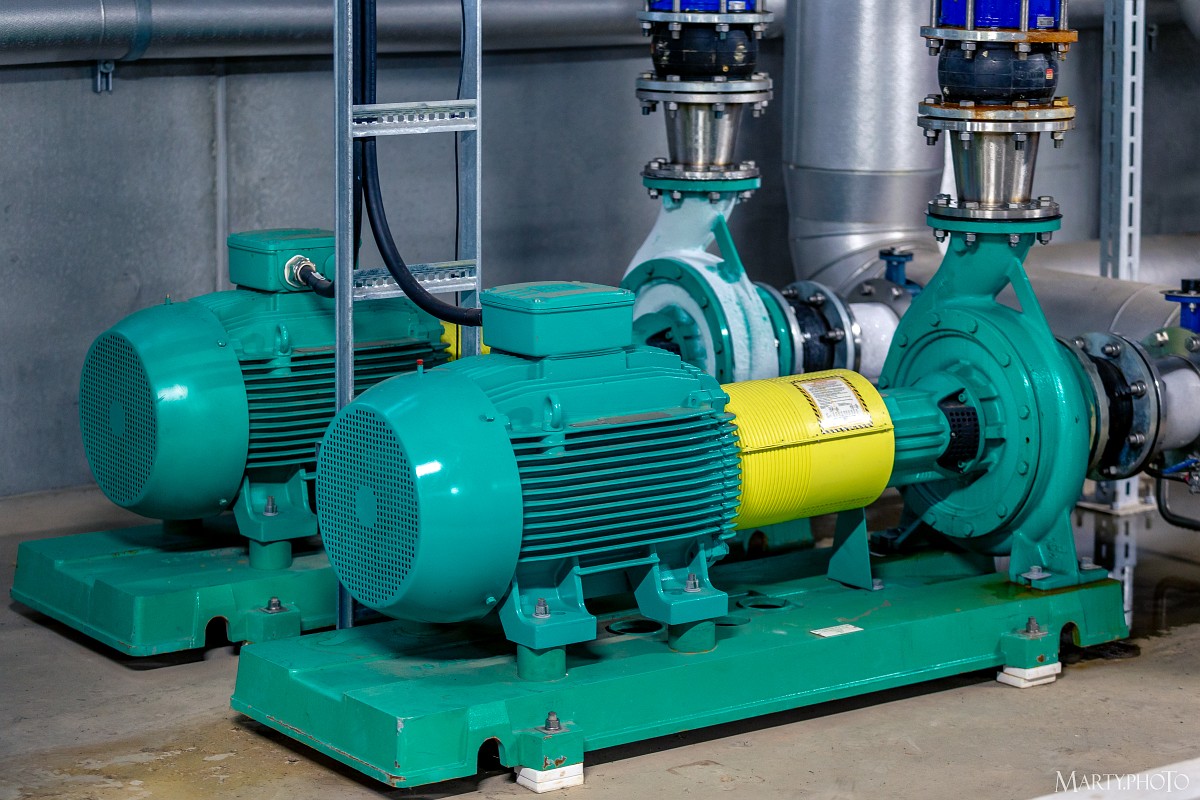
This refrigerated warehouse we designed for this client, incorporates a blast freezing facility within the refrigerated storage space. It includes rack blast freezing for carton-packaged meat. When not in use, the rack can be used for pallet storage as well.
What was particularly different about this project is The “cold lake” air distribution concept we employed as it relies on the differences in density between relatively cool and relatively warmer air.
As in any refrigerated warehouse, it is the circulating airstream that cools the space. The airstream does this by warming up slightly as it circulates throughout the facility. As the air warms, the density reduces, and the air seeks to rise towards the ceiling of the facility without requiring any mechanical assistance to do so.
From there, the air returns to the evaporator (air cooler) return, is refrigerated again and returned to the room. This is in contrast to the conventional air-distribution method, which injects relatively cold air at a high level into the refrigerated space, forcing the airstream to more or less do the opposite of what it naturally seeks to do when used as the cooling agent cooling the warehouse.
It also has abuent air defrost. Defrost is carried out by means of automatic motorised shutters. During defrost the cooling coil is isolated from the refrigerated warehouse on the airside, while ambient air is circulated through the cooling coil, causing it to defrost. This minimises heat ingress into the freezer during defrost.
The use of dry expansion refrigerant feed and the employment of evaporator materials with high thermal conductivities create a faster defrost cycle. The reason for this? Air coolers contain significantly less refrigerant at the commencement of the defrost, and warm up faster.
In the event of a refrigerant leak, the air cooler is forced into defrost mode. This prevents leaked refrigerant from entering the refrigerated space. Any ammonia exposure risk in the freezer(s) is further mitigated by the inherently lower operating refrigerant inventory in the air coolers of low-charge NH3 refrigerated systems. The operating evaporator refrigerant inventory is typically 30–50 times lower than conventional liquid overfeed ammonia plant.
The overall plant inventory is typically four to five times lower. To read the article in full click here.